Introduction
Understanding the true inkjet vs laser printer cost comparison requires looking far beyond the price tag at your local electronics store. While that $50 inkjet printer might seem like an obvious bargain compared to a $200 laser printer, the reality of printing costs unfolds over months and years of actual use, often revealing surprising truths that can save or cost you hundreds of dollars.
The question of which printer saves money becomes even more complex when you consider that manufacturers often use a business model similar to razor companies—selling the device cheaply while making profits on replacement supplies. This means the sticker price represents just the tip of the iceberg when calculating your true printing expenses over time.
This comprehensive analysis will walk you through every aspect of printer costs, from upfront investments to hidden expenses you might never have considered, helping you make an informed decision that aligns with both your budget and printing needs.
What Is the True Cost Structure of Modern Printing?
When we examine printer economics, we’re really looking at a complex ecosystem of interconnected costs that extend far beyond the initial purchase. Think of printer ownership like owning a car—the purchase price is just the beginning of your financial commitment, with ongoing fuel, maintenance, and operational costs determining the real expense over time.
The total cost of ownership for any printer includes several key components that work together to determine your actual expense per page. The initial hardware investment represents your entry fee into the printing world, but this cost gets spread across every page you print throughout the device’s lifetime. Replacement supplies, primarily ink cartridges for inkjets and toner cartridges for laser printers, typically represent the largest ongoing expense and vary dramatically between printer types and usage patterns.
Beyond the obvious costs lie several hidden expenses that can significantly impact your budget. Paper costs vary depending on quality requirements, with photo paper and specialty media commanding premium prices. Energy consumption, while seemingly minor, adds up over time and varies considerably between printer technologies. Maintenance costs, including cleaning supplies and occasional service calls, contribute to the overall expense picture.
Understanding this cost structure helps explain why manufacturers can afford to sell printers at seemingly low prices—they’re investing in a long-term relationship where replacement supplies provide ongoing revenue streams. This business model creates both opportunities and pitfalls for consumers, depending on how well they understand and navigate the total cost equation.
5 Critical Steps to Calculate Real Printer Costs
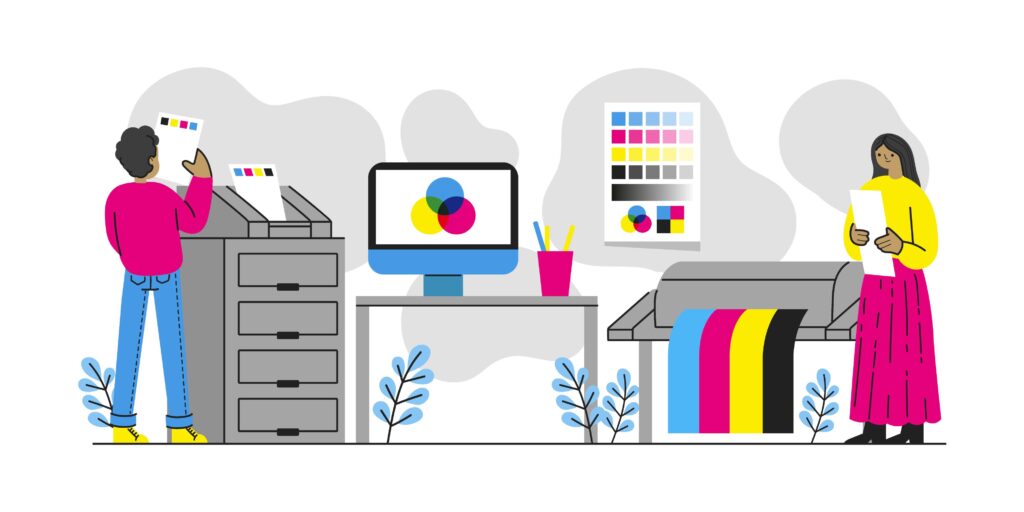
Step 1: Analyze Your Printing Volume and Patterns
Before diving into cost comparisons, you need to establish a baseline understanding of your actual printing behavior. Most people dramatically underestimate or overestimate their printing needs, leading to poor purchasing decisions that waste money. Start by tracking your printing for at least one month, noting both the quantity and types of documents you produce.
Separate your printing into categories: black and white text documents, color documents, photos, and specialty items like labels or envelopes. This breakdown becomes crucial because different printer types excel at different tasks, and the cost per page varies significantly across these categories. A typical home user might print 50-100 pages monthly, while a small business could easily exceed 500 pages, fundamentally changing the cost equation.
Step 2: Compare Upfront Investment Requirements
The initial purchase price creates your first decision point, but understanding what you’re actually buying helps justify the investment. Entry-level inkjet printers typically cost between $30-100, offering basic functionality suitable for light usage. However, these budget models often come with starter cartridges containing minimal ink, requiring immediate replacement purchases that can double your initial investment.
Laser printers generally require higher upfront investments, typically ranging from $100-400 for home and small office models. This higher cost reflects more durable construction, faster printing speeds, and included toner cartridges that often contain enough supplies for hundreds or thousands of pages right out of the box.
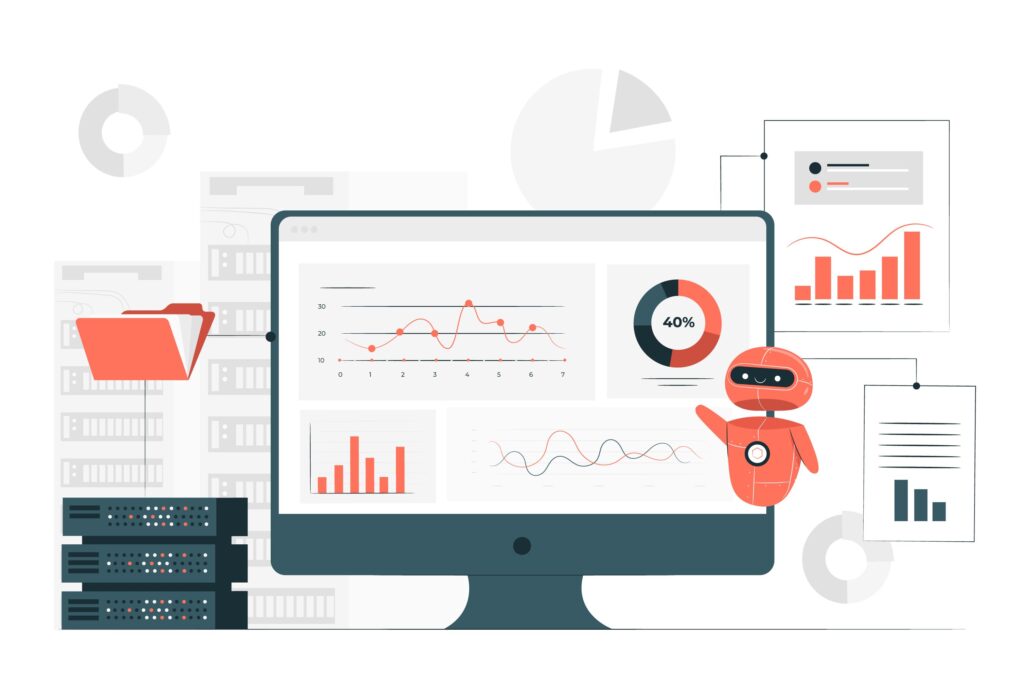
Step 3: Calculate Per-Page Costs Across Different Scenarios
This step requires some mathematical analysis, but the insights prove invaluable for making informed decisions. Manufacturers typically publish page yield estimates for their cartridges, though these numbers often reflect ideal conditions rather than real-world usage. For inkjet printers, black ink cartridges might yield 200-400 pages, while color cartridges often produce fewer pages due to the coverage requirements of typical color documents.
Laser printer toner cartridges generally offer much higher page yields, often producing 1,000-3,000 pages per cartridge. When you divide cartridge replacement costs by page yields, laser printers typically deliver black and white printing at 2-4 cents per page, while inkjets often cost 5-15 cents per page for similar documents.
Step 4: Factor in Reliability and Replacement Cycles
Printer reliability directly impacts your total cost of ownership through replacement frequency and maintenance requirements. Inkjet printers, with their complex liquid ink delivery systems, tend to require more frequent maintenance and have shorter lifespans, especially when used infrequently. Dried ink can clog print heads, requiring expensive cleaning cycles or even complete cartridge replacement.
Laser printers, built around more robust mechanical and electronic systems, typically operate reliably for years with minimal maintenance. Their solid toner particles don’t dry out during periods of non-use, making them ideal for intermittent printing scenarios. This reliability translates into lower long-term replacement costs and fewer frustrating downtime experiences.
Step 5: Evaluate Hidden Costs and Convenience Factors
Several less obvious costs can significantly impact your total printing expenses. Energy consumption varies dramatically between printer types, with laser printers typically using more power during printing but entering efficient sleep modes between jobs. Inkjet printers consume less power during printing but often require more frequent cleaning cycles that waste both ink and electricity.
Paper costs deserve careful consideration, especially if you plan to print photos or use specialty media. Inkjet printers generally handle a wider variety of paper types and thicknesses, while laser printers work best with standard office papers. Photo printing represents a particular cost consideration, as quality photo paper can cost 50 cents or more per sheet, making the per-print cost calculation quite different from standard document printing.
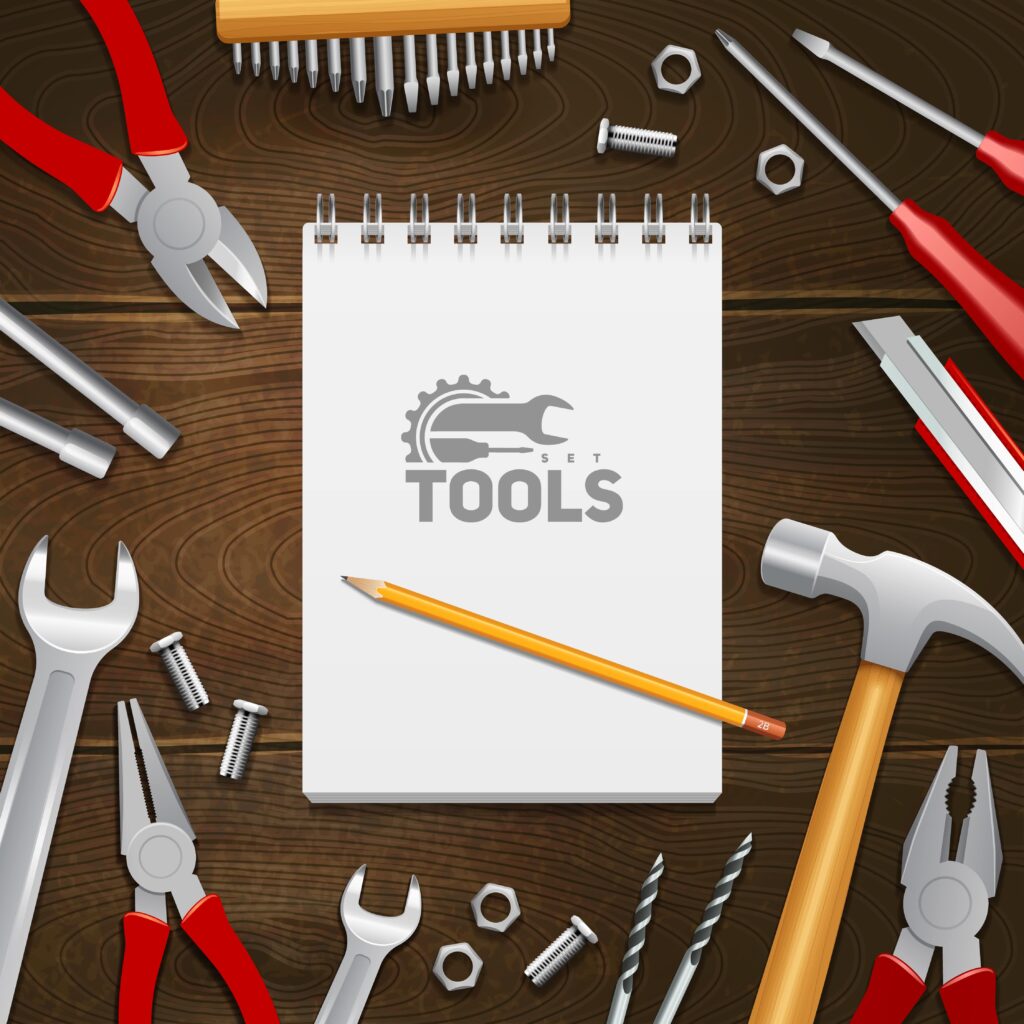
Advanced Cost Analysis Tools and Techniques
Professional buyers often use sophisticated models to evaluate printer costs, and these same techniques can benefit individual consumers making important purchasing decisions. The concept of net present value applies to printer purchases, where you calculate the total cost of ownership over a specific time period, then discount future costs to present value terms.
Online calculators provided by manufacturers and independent testing organizations can help automate these calculations, though you should verify their assumptions against your actual usage patterns. Some calculators allow you to input your specific printing volumes, local supply costs, and energy rates to generate personalized cost projections.
Third-party ink and toner suppliers add another dimension to cost analysis, potentially reducing ongoing supply costs by 30-70% compared to original manufacturer cartridges. However, these savings come with potential risks including warranty concerns, quality variations, and compatibility issues that could affect your total cost calculation.
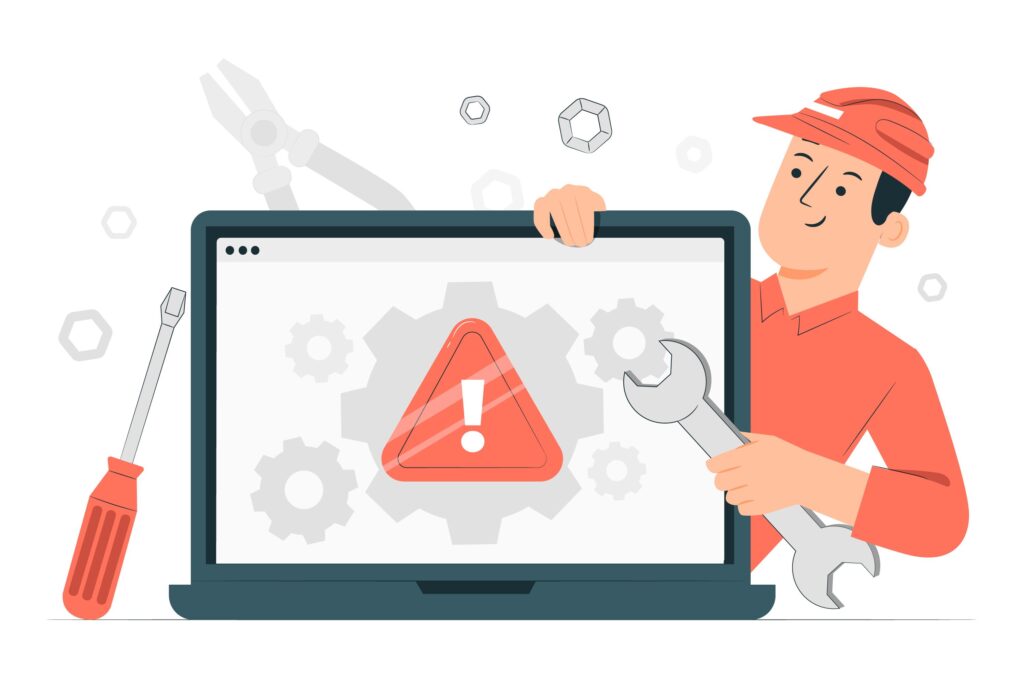
Common Printer Cost Calculation Mistakes and How to Avoid Them
Many consumers fall into predictable traps when evaluating printer costs, leading to decisions they later regret. The most common mistake involves focusing exclusively on upfront costs while ignoring ongoing expenses. This shortsighted approach often results in choosing printers with low purchase prices but astronomical operating costs that quickly overwhelm any initial savings.
Another frequent error involves miscalculating actual printing volume, either overestimating needs and buying expensive high-capacity printers that sit largely unused, or underestimating requirements and purchasing inadequate devices that struggle with actual workloads. Accurate volume estimation requires honest assessment of current printing habits and realistic projections of future needs.
Quality requirements represent another area where poor planning leads to cost surprises. Choosing a basic inkjet printer for occasional photo printing seems economical until you discover that acceptable photo quality requires expensive photo paper and premium ink cartridges, making each photo cost several dollars to produce.
Frequently Asked Questions
Which is cheaper to run: inkjet or laser printer? For high-volume black and white printing, laser printers typically cost 2-4 cents per page compared to 5-15 cents for inkjets. However, for low-volume color printing and photos, inkjets can be more economical due to their lower upfront costs.
How do I calculate the real cost per page? Add the printer price divided by expected lifetime pages to the cartridge cost divided by cartridge page yield. Include paper costs and estimated maintenance expenses for the most accurate calculation.
Do generic cartridges really save money? Generic cartridges can reduce supply costs by 30-70%, but may affect print quality and printer warranty coverage. Calculate potential savings against these risks based on your specific needs and risk tolerance.
When does a laser printer become more economical than inkjet? Generally, when you print more than 100 pages monthly, laser printers become more cost-effective due to their lower per-page costs, despite higher upfront investments.
Conclusion
The inkjet vs laser printer cost analysis reveals that true savings depend entirely on understanding your specific printing patterns and calculating total ownership costs rather than focusing solely on purchase prices. While inkjet printers offer lower entry costs and superior photo quality, laser printers deliver significant long-term savings for users with moderate to high printing volumes, particularly for text documents.
The key to making the right choice lies in honest assessment of your printing needs, careful calculation of per-page costs using realistic supply prices, and consideration of factors like reliability and convenience that affect your total cost of ownership. Remember that the cheapest printer to buy is rarely the cheapest printer to own, and investing time in proper analysis can save you hundreds of dollars over your printer’s lifetime while ensuring you get the performance you actually need.
How to Choose the Right Printer for Your Home or Office in 2025 Read More.
Recent Comments